When it comes to working with sheet metal, precision and efficiency are paramount. Whether you’re crafting intricate designs or assembling structural components, mastering the art of sheet metal fabrication can make a world of difference in the quality of your work. Every step, from measuring and cutting to bending and welding, requires careful attention to detail to ensure a perfect fit and finish.
This guide will explore tips and techniques to help you achieve precision and efficiency in your sheet metal projects. Whether you’re a seasoned professional or just starting, these insights can help you take your skills to the next level and produce high-quality, professional results.
Understanding Sheet Metal Types and Properties
Sheet metal comes in various types and grades, each with unique properties and applications. Common types include stainless steel, aluminum, and copper, each offering strengths, corrosion resistance, and aesthetic qualities. Understanding these properties is crucial to selecting the suitable material for your project.
For example, stainless steel is ideal for high strength and durability applications, while aluminum is lightweight and corrosion-resistant, making it suitable for aerospace and marine industries. Understanding these differences allows you to choose the most suitable material for your project, ensuring optimal performance and longevity.
Essential Tools for Sheet Metal Work
When working with sheet metal, having the right tools is essential for achieving precision and efficiency. Whether cutting, bending, or forming, using the appropriate equipment ensures high-quality results and simplifies the fabrication process.
- Shears: These are crucial for cutting sheet metal to size. Available in various types, such as manual, electric, and pneumatic, shears provide clean, straight cuts for different sheet metal thicknesses.
- Brakes: Used for bending sheet metal, brakes come in different varieties, such as box-and-pan brakes, cornice brakes, and hydraulic brakes. They allow for precise angles and intricate bends, which are essential for creating custom shapes and structures.
- Rollers: Rollers are used to form sheet metal into curves and cylinders. They are essential for projects requiring rounded shapes, offering consistent and smooth bends.
- Measuring Tools: Accurate measurements are vital in sheet metal work. Tools such as calipers, rulers, and protractors ensure precise dimensions and angles, helping to avoid costly mistakes and rework.
- Safety Equipment: Working with sheet metal can be hazardous, so safety equipment like gloves, goggles, and ear protection is crucial. These protect against sharp edges, flying debris, and loud noises, ensuring a safe working environment.
Incorporating these essential tools into your sheet metal work will enhance efficiency and precision, yielding superior quality and craftsmanship in your projects.
Proper Measurement Techniques for Accuracy
Accurate measurements are crucial in sheet metal work to ensure a precise fit and finish. Using the right tools and techniques can make a big difference in the quality of your work. Always use a straight edge when measuring sheet metal to ensure straight cuts and angles.
Additionally, consider using a scribe or marker to mark your measurements before cutting to ensure accuracy. Double-check your measurements before cutting or bending to avoid costly mistakes and rework. You can achieve the precision and accuracy needed for high-quality sheet metal work by following proper measurement techniques.
Precision Cutting Methods for Clean Edges
Achieving clean edges in sheet metal work is vital for a professional and polished finish. Precision cutting methods ensure these clean edges, providing both accuracy and efficiency.
- Shearing: This traditional method uses a sharp blade to cut through the metal, providing straight and clean edges with minimal deformation.
- Laser Cutting: This method utilizes a high-powered laser beam to melt the metal precisely, resulting in accurate cuts with minimal heat-affected zones.
- Waterjet Cutting: A high-pressure stream of water mixed with abrasive particles cuts through the metal, offering high precision and versatility without generating heat.
- Plasma Cutting: This technique uses a jet of ionized gas at high temperatures to cut through the metal, which is suitable for thicker materials and provides clean cuts with a smooth finish.
- Punching: In this method, a punch press creates precise holes and shapes in the metal, ensuring clean edges and accurate dimensions.
By selecting the appropriate precision cutting method for your specific project requirements, you can achieve clean, professional edges that enhance the overall quality and appearance of your sheet metal work.
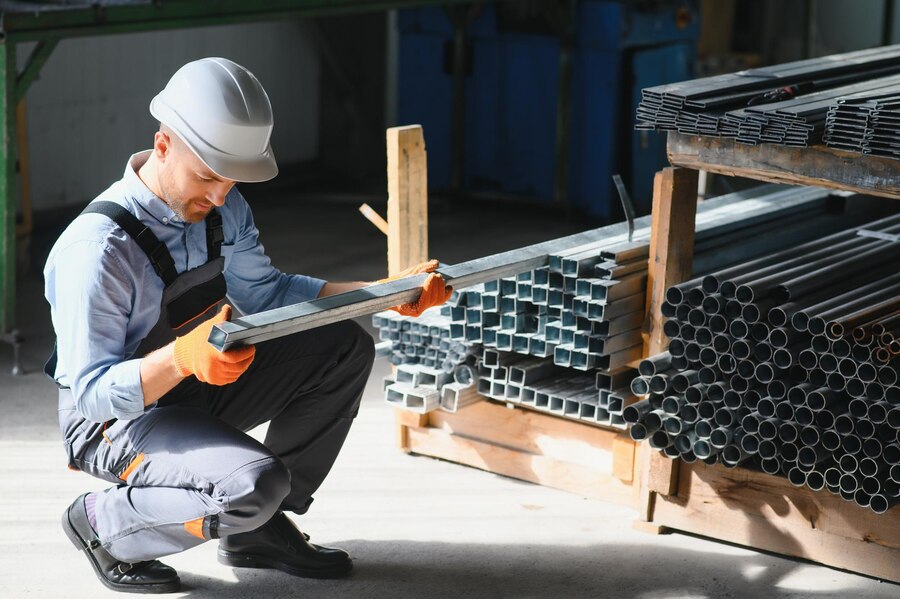
Efficient Bending and Forming Techniques
Bending and forming are standard sheet metal work techniques to create complex shapes and structures. Several methods can bend and form sheet metal, including brake press, roll forming, and stretch forming. A brake press is a standard tool that uses a punch and die to bend the metal at a specific angle.
Roll forming uses a series of rollers to bend the metal gradually into the desired shape. Stretch forming involves stretching the metal over a form to create complex curves and shapes. Using efficient bending and forming techniques, you can achieve the desired shapes and structures in your sheet metal projects precisely and efficiently.
Welding Tips for Strong and Clean Joints
Welding is often used in sheet metal work to join pieces together. Proper welding techniques are essential to creating strong, clean joints that are free from defects. When welding sheet metal, it’s crucial to use the right welding process and filler material for the type of metal being welded.
Additionally, proper preparation of the metal surfaces, such as cleaning and deburring, is essential to ensure a strong weld. Controlling heat input and welding speed is also critical to prevent warping and distortion of the metal. These welding tips can create solid and clean joints in your sheet metal projects.
Finishing Touches: Deburring and Surface Treatment
After cutting, bending, and welding, sheet metal often requires finishing touches to remove sharp edges and improve its appearance. Deburring is the process of removing burrs or rough edges from the metal, typically done using a deburring tool or file.
Surface treatment, such as painting, powder coating, or anodizing, can also improve the metal’s appearance and protect it from corrosion. These finishing touches enhance the aesthetics of your sheet metal projects and also improve their durability and longevity.
Handling and Storage Best Practices
Proper handling and storage of sheet metal are crucial to maintaining its quality and preventing damage. Following best practices can help ensure that your sheet metal remains in top condition for your projects, reducing waste and saving costs.
- Use Gloves for Protection: Always wear gloves when handling sheet metal to protect yourself from sharp edges and avoid injury.
- Handle with Care: Gently lift and move sheet metal to avoid bending, denting, or scratching the surface.
- Store in a Dry Area: To prevent corrosion and rust, keep sheet metal in a dry, well-ventilated area. Moisture can quickly degrade the material.
- Keep Flat: Store sheet metal flat to maintain shape and prevent warping or bending. Avoid stacking heavy objects on top.
- Organize by Type and Size: Organize your sheet metal by type and size to quickly find the right piece when needed and prevent damage from searching through stacks.
By following these best practices for handling and storage, you can ensure that your sheet metal is always ready for use, maintaining its quality and extending its lifespan. Implement these tips to keep your materials pristine for all your projects.
Safety Precautions for Sheet Metal Work
Sheet metal work poses safety risks, such as sharp edges, flying debris, and hot surfaces. Proper safety precautions are essential, such as wearing protective gear such as gloves, goggles, and ear protection.
Use tools and equipment correctly, following manufacturer guidelines. Keep your workspace clean and well-ventilated to avoid tripping hazards and exposure to fumes. Prioritizing safety helps prevent accidents and injuries.
Troubleshooting Common Sheet Metal Issues
Troubleshooting common sheet metal issues is essential for maintaining the quality and integrity of your projects. Whether you’re dealing with warping, distortion, or cracking, identifying and addressing these problems early can save time and resources.
- Warping: This often occurs due to excessive heat during welding. Proper welding techniques must be used to prevent it, and heat input must be controlled. If warping has already occurred, it can sometimes be corrected by applying controlled heat in the opposite direction.
- Distortion: Similar to warping, distortion is typically caused by uneven heating. Ensuring uniform heat distribution and using clamps to hold the sheet metal during welding can minimize this issue.
- Cracking: Cracking can happen due to high-stress concentrations or improper material selection. Using the appropriate filler material and ensuring the metal is not under excessive stress can help prevent this.
- Rough Edges: Rough edges are often a result of dull cutting tools. Keeping your tools sharp and using the correct cutting method for the type of sheet metal can produce smoother edges.
- Surface Defects: Scratches or dents can occur during handling and storage. Using protective coverings and handling the sheet metal with care can reduce the likelihood of surface defects.
Addressing these common sheet metal issues ensures that your projects maintain their structural integrity and professional appearance.
Mastering sheet metal work requires knowledge, skills, and the right tools. Understanding the types and properties of sheet metal is crucial for selecting the suitable material for your project, ensuring optimal performance and longevity. Essential tools such as shears, brakes, and rollers are necessary for cutting, bending, and forming sheet metal precisely and efficiently.
Proper measurement techniques are essential for accurate cuts and bends, while precision cutting methods like shearing and laser cutting can achieve clean edges. Efficient bending and forming techniques and proper welding tips help create strong and clean joints in your sheet metal projects.
Finally, finishing touches such as deburring and surface treatment, along with proper handling, storage, and safety precautions, are essential for maintaining the quality and integrity of your sheet metal work. Iron Range Plumbing & Heating Inc. at 218-262-2315 can provide expert advice and services for all your sheet metal needs. Call us today for assistance with your sheet metal projects.